
PCB Capability
GENERAL PARAMETERS | ||||
---|---|---|---|---|
Manufacturing Materials | Capability | |||
Material Brand | KB,TUC,EMC,MGC,ITEQ,SYTECH,Rogers,Arlon,Nanya,Isola,Nelco,Taconic,Panasonic,Ventec,Dupond,Taiflex,etc. | |||
FR4 | Tg135: KB6160, S1141, TU662 | |||
Tg150: KB6165, S1000H, IT158 | ||||
Tg170: KB6167, S1000-2M, IT180A, TU768 | ||||
Halogen Free FR4 | Tg150: S1150G | |||
Tg170: S1170G, TU862HF | ||||
High CTI(CTI≥600) | KB-6160C, S1600L, S1151G(Halogen Free) | |||
Ceramic Filling High Frequency Material | Rogers 4003C/4350B, Arlon25N, S7136H, WL-CT350 | |||
PTFE High Frequency Material | Rogers Series, Arlon Series, Taconic Series, F4BM Series, Teflon,etc. | |||
High Speed Material | TU-872SLK/SLK-SP, TU883/933, Panasonic Megtron4/Megtron6/Megtron7, Isola FR408HR | |||
Rigid PI Material | Arlon 85N, VT901 | |||
Metal Base Board | Bergquist Al base, Chinese Brand Al base, Copper base | |||
BT Materials For Chip-LED | CCL-HL820WDI, SY-WLM1 | |||
BT Materials for IC Plastic Package | CCL-HL832NS, CCL-HL832NSR, CCL-HL832NSF, GHPL-830SR, CCL-HL972LFG, SI10US | |||
Material Mixed Laminate | 4 layers – 48 layers (FR4 + High Frequency/Speed Material, FR4 + Metal Base, FR4 + FPC) | |||
Special PP | NFPP: Arlon 49N, VT47 | |||
Ceramic Filling PP: Rogers 4450F | ||||
PTFE PP: Arlon 6700, Taconic FR-27 | ||||
BT PP:GHPL-830NS, GHPL-830NSR, GHPL-830SR, GHPL-970LFG | ||||
Note | Other special materials can be processed and produced by means of customer supply or purchasing. | |||
Item | Standard | Advanced | Innovative | |
IC Space(Green Color) | 4 | 4 | 3 | |
IC Space(Other Color) | 5 | 5 | 4 (blue oil) | |
Liquid Photoimageable(LPI)Solder Mask Registration | 3mil | 2mil | 1.5mil | |
Thickness T>1.0 mm | ±10% | ±8% | ±5% | |
Tolerance T≤1.0 mm | ±0.1 | ±0.1 | ±0.05 | |
Board Thickness (mm) | 0.5-5.0 | 0.25-6.5 | 0.1-10 | |
Hole Aspect Ratio | 10:1 | 12:1 | 20:1 | |
Via Size For Plug Solder Mask | 0.25-0.5 | 0.20-0.5 | 0.15-0.6 | |
Via Size For Plug Resin And Capped Copper | 0.25-0.5 | 0.20-0.5 | 0.075-0.6 | |
Panel Size (mm) | 457×609 | 457×609 | 609×1200 | |
Bow And Twist | ≤0.75% | ≤0.75% | ≤0.5% | |
INNER GRAPHICS | ||||
Item | Basic copper thickness | Line Width/Space | ||
Minimum Inner Line Width Distance | 1/3 OZ | 2/2 | ||
0.5 OZ | 2.5/2.5 | |||
1.0 OZ | 3/3 | |||
2.0 OZ | 5/5 | |||
3.0 OZ | 7/7 | |||
4.0 OZ | 9/9 | |||
5.0 OZ | 10/16 | |||
6.0 OZ | 10/10.5 | |||
10 OZ | 18/20 | |||
12 OZ | 22/24 | |||
Hole to Line Spacing | 4 layers | ≥3mil(1 core) | ||
6 layers | ≥5mil(2 core) | |||
8 layers | ≥7mil(3 core) | |||
10 layers and above | ≥7mil | |||
Line Width/Space Accuracy | Non-impedance plate ±20%; Impedance plate ±10% | |||
Alignment Accuracy | ±25um(CCD) | |||
OUTER GRAPHICS | ||||
Item | Basic copper thickness | Line Width/Space | ||
Minimum Outer Line (mil) | 1/3 OZ | 2.5/2.5 | ||
0.5 OZ | 2.8/2.8 | |||
1.0 OZ | 3/3 | |||
2.0 OZ | 5/5.5 | |||
3.0 OZ | 6/7.5 | |||
4.0 OZ | 14/12 | |||
5.0 OZ | 18/17 | |||
6.0 OZ | 13/11 | |||
10 OZ | 16/26 | |||
12 OZ | 24/32 | |||
The Minimum Line Width Of The Outer Etched Word | Base Copper H OZ; 8mil | |||
Base Copper 1 OZ; 10mil | ||||
Base Copper 2 OZ; 12mil | ||||
Line Width/Space Accuracy | Non-impedance plate ±20%; Impedance plate ±10% | |||
Alignment Accuracy | ≤24um(LDI) | |||
HOLE PROCESSING | ||||
Item | Mass Production | Prototyping | ||
Through Hole | Hole Diameter (max) | 6.5mm, thickness <6.4mm | Greater than 6.5mm (hole expansion process) | |
Hole Diameter (min) | 0.15mm,thickness<1.0mm | 0.15mm, thickness<1.6mm | ||
Hole Tolerance | NPTH±0.05mm, PTH hole±0.075mm, crimping hole±0.05mm | |||
Hole Tolerance | ±0.05mm | |||
Thickness Ratio | 8:1 | 20:1 | ||
Minimum Hole Spacing | The same grid > 8mil Non-same grid ≥ 12mil | The same grid ≥ 6mil Non-same grid ≥ 10mil |
||
Deep Hole Control | Minimum Depth Control Hole Diameter | 0.155mm | ||
Depth Control Accuracy | 0.1mm | 0.05mm | ||
Hole Depth Thickness Diameter Ratio | ≤0.6:1 | ≤0.8:1 | ||
Control Depth Groove Depth Tolerance | ±0.15mm | ±0.1mm | ||
Stepped Hole | Step Hole Diameter Tolerance | 0.1mm | 0.05mm | |
Step Hole Depth Tolerance | 0.2mm | 0.1mm | ||
Laser Hole | Laser Hole Copper | ≥10um | ||
Hole Diameter Range | 0.1mm-0.15mm | 0.076mm-0.15mm | ||
Laser Blind Hole Thickness To Diameter Ratio | ≤0.6:1 | ≤0.8:1 | ||
Outer Line Width And Line Spacing | 3.5/4mil | 3.5/3.5mil | ||
Inner Line Width And Line Spacing | 3.0/3.5mil | 3.0/3.3mil | ||
Laser Blind Hole Medium Thickness | 2.5-4mil | 2.5-5mil | ||
Back Drilling | Depth Tolerance | ±0.1mm | ||
Position Tolerance | ±0.1mm | |||
Hole To Outer Line Distance | ≥0.15mm | ≥0.125mm | ||
Hole To Inner Line Distance | ≥0.175mm | ≥0.15mm | ||
Countersunk Hole | Countersunk Drill Diameter | The 45° countersunk bit has a diameter of 4.5mm | ||
60°, 82°, 90° countersunk bit diameter is 6.35mm | ||||
100° countersunk bit diameter is 6.5mm | ||||
Outer Aperture Accuracy | ±0.2mm | |||
PTH Countersunk Ring Width | 8mil | |||
PTH Countersunk Hole Distance Line | 12mil | |||
Conical Hole | Opening Tolerance | ±0.2mm | ||
Aperture Angle | 45°、60°、90° | |||
Slot | Minimum Slot | 0.5mm | ||
OUTLINE | ||||
Item | Mass Production | Prototyping | ||
V-CUT | Angle | 20°、30°、45°、60° | ||
Jumping Knife Distance | ≥8 mm | |||
Board Thickness | 0.4 mm-3.0mm | |||
Thickness Accuracy | ±0.1 mm | ±0.05 mm | ||
Gong Board | Minimum Gong Cutter Diameter | 0.6 mm | ||
Control Deep Gong Plate Thickness | ≥0.4 mm | |||
Depth Tolerance Of Deep Gong Plate | ±0.15 mm | ±0.1 mm | ||
Tolerance Of Deep Gong Plate Size | ±0.13 mm | |||
Hypotenuse | The Outer Layer Of The Top Of The Gold Finger Is Copper | Bevel depth +0.2 mm | ||
The Inner Layer Of The Top Of The Gold Finger Is Copper | Bevel depth +0.4 mm | |||
Angle (tolerance ±5°) | 20°, 30°, 45°, hypotenuse angle is usually 30° | |||
SURFACE TREATMENT | ||||
Item | Standard | Advanced | Innovative | |
ENIG | Nickel Thickness (um) | 2.0-5.0 | 3.0-5.0 | 3.8-7.62 |
Gold Thickness(uinch) | 1.0-2.0 | 2.0-3.0 | 3.0-5.0 | |
Hard Gold (Au Thickness) | Normal Golden Finger(um) | 0.15 | 0.8 | 3.0 |
Selective Hard Gold (um) | 0.15 | 0.8 | 2.0 | |
ENEPIG | Nickel Thickness (um) | 2.0-5.0 | ||
Palladium Thickness(uinch) | 4.0-20.0 | |||
Gold Thickness(uinch) | 1.0-5.0 | |||
Plating Gold | Nickel Thickness (um) | 2.0-7.62 | ||
Gold Thickness(uinch) | 1.0-5.0 | |||
Immersion Tin | Tin Thickness (um) | 0.8-1.2 | ||
Immersion Silver | Sliver Thickness (um) | 0.15-0.4 | ||
OSP (um) | 0.2-0.6 | |||
Tin Lead HASL (um) | 2.0-40.0 | |||
Lead Free HASL (um) | 2.0-40.0 | |||
Note:Tin Lead /LF HASL panel size should less than ≤500×600 mm,thickness≥0.6 mm;Hard Gold panel size≤400×500 mm,the other surface treatment panel size less than 500×900 mm | ||||
SPECIAL PROCESS | ||||
Item | Standard | Advanced | Innovative | |
Back Drilling | YES | YES | YES | |
Heavy Copper PCB with Blind/Burried Via | YES | YES | YES | |
N + N Structure | YES | YES | YES | |
POFV(VIPPO) | YES | YES | YES | |
Long-Short Gold Finger | YES | YES | YES | |
Buried Capacitance/Resistance | YES | YES | YES | |
Plated Half Holes/Edge Plating | YES | YES | YES | |
Soft Bondable Gold | YES | YES | YES | |
Embedded Daughter Board | YES | YES | YES | |
Embedded Magnetic Cores | YES | YES | YES | |
PTH/NPTH Step Slots | YES | YES | YES | |
Step Gold Finger | YES | YES | YES | |
Graph In Bottom Of Step | YES | YES | YES | |
Post Bonding | YES | YES | YES | |
Sweat Soldering | YES | YES | YES | |
Embedded Coin/Ceramic | YES | YES | YES | |
High Depth Laser Hole | YES | YES | YES | |
Double Side Press Fit Hole | YES | YES | YES | |
Hybrid Material Lamination(Local Hybrid) | YES | YES | YES | |
DELIVERY ABILITY | ||||
1-2L Lead-time | Sample Expedited 8 hours, Normal 2-3 days, Mass production 5-7days | |||
4-8L Lead-time | Sample Expedited 24 hours , Normal 5-7days, Mass production 7-10 days | |||
10-18L Lead-time | Sample Expedited 48-72 hours, Normal 10-15 days,Special circumstances based on the actual PCB design | |||
More than 20L Lead-time | Normal 10-15 days ,Special circumstances based on the actual PCB design | |||
Acceptable File Format | ALL Gerber Files、POWERPCB、PROTEL、PADS2000、CAD、AUTOCAD、ORCAD、P-CAD、CAM-350、CAM2000 etc. | |||
Who is PEAK?
Founded in 2007, PEAK Co.,Ltd is an electronic solutions company offering 1-64 layers PCB fabrication, assembly, testing & validation of rigid, rigid-flex, HDI, high frequency, high speed, metal core, IC substrate, substrate-like and other special PCB. Our modern 54,000 square foot manufacturing facility allows us to provide all rigid & rigid-flex services under one roof and offer quick-turn capabilities.PEAK has a professional reputation for developing high-performance solutions for technically advanced OEM’s in a variety of markets including aerospace and defense, medical, computer, communication, server, semiconductor IC, automotives, industrial control, optoelectronics, LED and others.
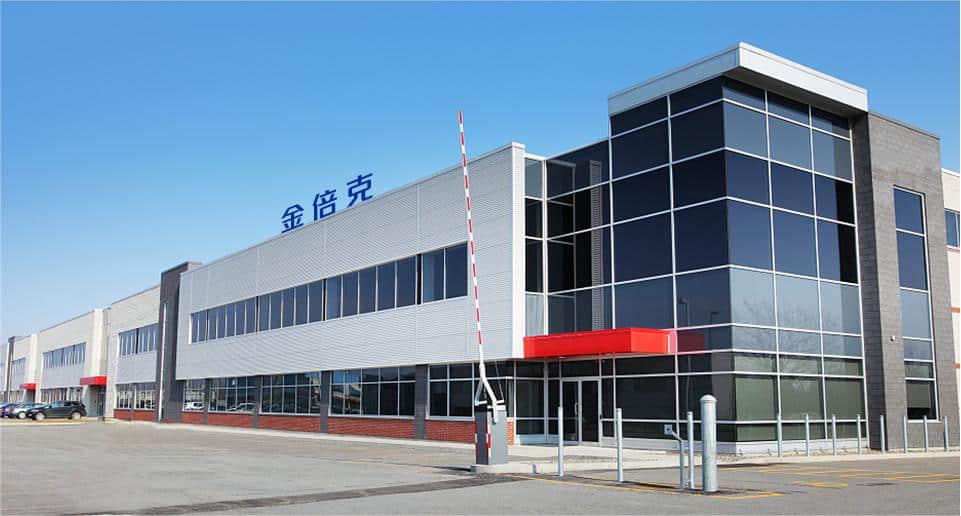

Ability to Handle Complex Jobs
All Rigid & Rigid-Flex Services Under One Roof
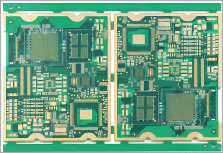
Regular PCB
Up to 64 Layers; FR4 TG135/TG150/TG170; Halogen Free/CTI≥600; Aspect Ratio (Finish Hole) 28:1; Sample Expedited 8 Hours(1-2Layer);
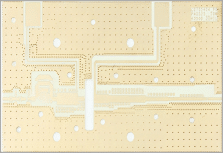
Metal Core PCB
Thermal Conductivity 1-398W/m.K; Aluminum/Copper AC 500-4000V; Post-bonding/Pre-bonding; Sweat-Soldering/Conductive Adhesive; Press-Fit/Embedded Coin(I, T U);

HDI PCB
Blind/Buried/Hybrid Via; 5+N(N+M)+5 Structure; Trace Width/Spacing 1.6/1.6mil; Laser Hole Size(mm)≥0.075; High Density Interconnector;
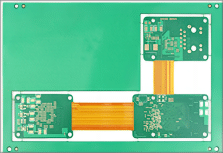
Rigid-Flex PCB
2-24 Layers; Book/Air-gap/Fly-tail; Unsymmetrical/Semi-Flex; Width of Flexible Zone 3mm(min); Dimension Accuracy ±0.05mm(min);
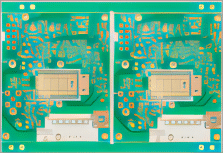
High Frequency PCB
More than 85+ Types; Rogers/Arlon/Taconic/Isola/ Nelco/F4B Serices,etc; Materials can be Specified; Impedance Tolerance ±5%(min);
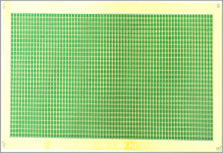
Substrate PCB
CSP/FC-CSP/SIP/FC-BGA/WB-CSP; FR4/BT/High-Speed Material; Trace Width/Space 12/12μm; SM Registration:±20μm; Strict SM Flatness Control ≤5μm;
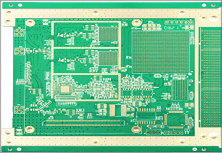
High Speed PCB
Panasonic Megtron4/6/7; TU-872SLK/Isola-FR408HR,etc; Impedance Tolerance ±5%(min); Dimension Accuracy ±0.02mm(min); Line Width/Space Accuracy ±5%;
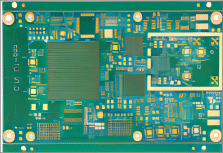
Specialty PCB
Ceramic/Glass Material; Hybrid Material Lamination; Buried Capacitance/Resistance; PTH/NPTH Step Slots; Uneven/Segmented/Step Gold Finger;
Check it out
The Complete Guide to Etching PCB – A Step-by-Step Process for DIY Enthusiasts PCB etching is an indispensable skill for creating custom printed circuit boards (PCBs) at home, giving DIY enthusiasts the power to design and fabricate PCBs without outsourcing fabrication services. In this guide, we’ll walk through each step of
The Ultimate Guide to Cleaning PCBs – Tips and Techniques for Effective Maintenance Printed circuit boards (PCBs) form the backbone of modern electronic devices. As they contain complex circuits, components, and solder connections that require regular cleaning and maintenance for optimal performance and reliability, PCBs need regular attention as part
Understanding Vias PCB Design: Importance, Types, and Implementation Vias are essential components of printed circuit board design, acting as conduits that connect electrical connections between layers of the printed circuit board. Vias serve an important function by maintaining signal integrity, power distribution and thermal management – something we will explore
Understanding PCB Stackup: Importance, Considerations, and Best Practices PCB stackup refers to the arrangement of layers on a printed circuit board (PCB), including conductors, dielectric layers and any necessary components. It plays an integral part in determining its electrical and mechanical performance; we will explore its importance here as well
Exploring the Global (Printed Circuit Board) PCB Market: Trends, Growth, and Opportunities The printed circuit board (PCB) market plays an integral part of global electronics manufacturing. PCBs are intricately crafted boards used to connect and support electronic components. In this article, we’ll take an in-depth look at this global PCB
A Guide to PCB Repair: Tips and Techniques for Fixing Printed Circuit Boards Printed circuit boards (PCBs) are key components of electronic devices, providing connections for components to communicate and function efficiently. Unfortunately, PCBs may sometimes encounter issues that necessitate repairs; we will provide an extensive guide to PCB repair
Exploring OrCAD PCB Design Software for Efficient Circuit Board Development OrCAD PCB is an innovative design software used extensively in the electronics industry for efficient circuit board development. Thanks to its advanced features and user-friendly interface, OrCAD PCB enables designers to efficiently design complex layouts while validating designs and optimizing
DigiKey PCB Services – Streamlining Your PCB Prototype and Assembly Process Digi-Key Electronics is a globally trusted distributor of electronic components and provides an array of products and services tailored to the needs of engineers, designers, hobbyists, hobbyists and more. One such offering by Digi-Key is PCB services which provide
Mastering the Art of Soldering PCBs – Tips for Successful Assembly Soldering is an integral step in the assembly of printed circuit boards (PCBs), as it creates electrical connections essential for electronic component functioning. Mastering soldering is key for creating reliable connections; in this article we’ll cover techniques and best